
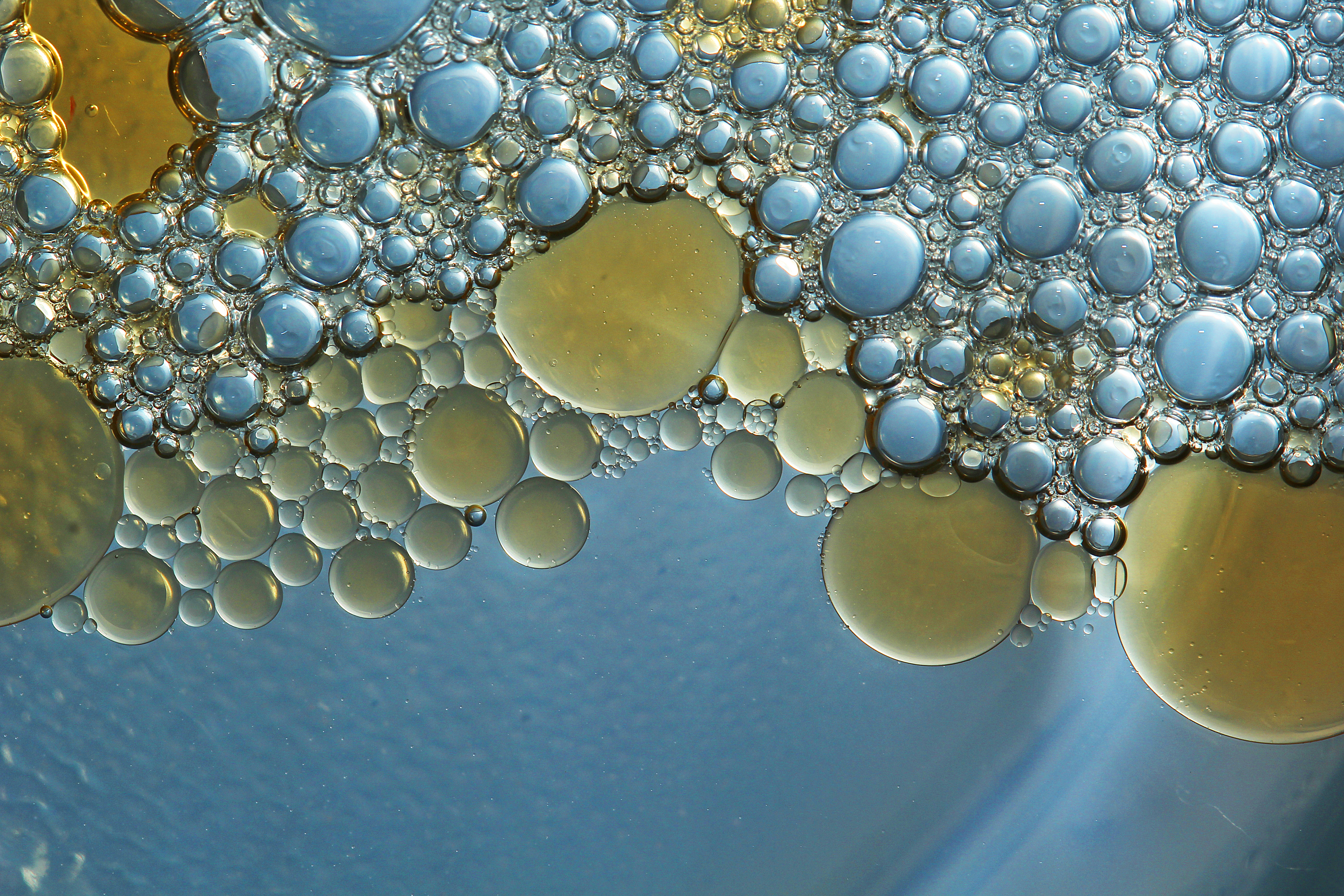
The results showed that the optimum process conditions are: emulsifier dosage, 0.5% oil to water ratio, 1:1 stirring intensity, 2500 rpm and mixing temperature, 30 ☌. Two liquids can form different types of emulsions.

The variables studied include emulsifier dosage, ratio of oil to water, stirring intensity, emulsifying temperature and mixing time. The emulsion was prepared using 100 ml colloid mill with sorbitan monooleate (SM) as emulsifier. However, there are some applications which require. Small droplets of oil are dispersed in water to. Oil Water Separators (OWS) are an effective technology in most oil-water separation applications. The present study was undertaken to experimentally investigate the effects of different process variables on emulsion stability. An oil-in-water emulsion is a mixture in which an oily medicine is dispersed in water or other liquid. Compared with normal emulsions, double emulsions have two oil-water interfaces, which can provide better protection to bioactive compounds and increase their resistance to degradation by the external phase. The preparation of stable water-in-oil (W/O) emulsion is critical for the success of production of stable coal–oil–water slurry. It has lower viscosity, lower ignition point and higher heating value than coal–water slurry. The coal–oil–water slurry is a new type of oil-based synfuel composed of finely pulverized coal, oil and water. There has been much interest in alternative fuels made from coal which is much more abundant than oil. The optimum processing conditions for preparing W/O/W emulsions are as follows: the ratio of the oil phase to the internal water phase is 80 : 20, the. A colloidal system in which one liquid is dispersed in another liquid immiscible with it is called an emulsion.
